|
 |
MILLER FILTER
|
 |
 |
|
HISTORY OF MILLER FILTER DEVELOPMENTS - PATENTED INNOVATIONS AND REALISATIONS -
|
 |
Contents of this chapter:
|
|
|
 |
SEVENTIES 1975 - 1980: THE SIMPLE DESIGN
|
 |
|
 |
SEVENTIES: BASIC PATENT
|
 |
 |
|
United States Patent Miller (19) 4,233,157 Nov. 11. 1980 „Travelling Sheet Flat Bed Filter Apparatus and System”
|
 |
EIGHTIES: 1980 - 1986: FURTHER IMPROVEMENT OF THE ORIGINAL CONCEPT / PATENT
|
 |
|
|
|
 |
EIGHTIES: 1987 - 1993: The SEALED SYSTEM / PATENT
|
 |
 |
|
The reversing band design of the previous development period was successful for a range of niche applications in a variety of industries but failed to find widespread acceptance in the liquid processing industries. This was mainly due to
- The exposed design
and
- The unsuitability of reversing storage rolls of media in the chemical industry
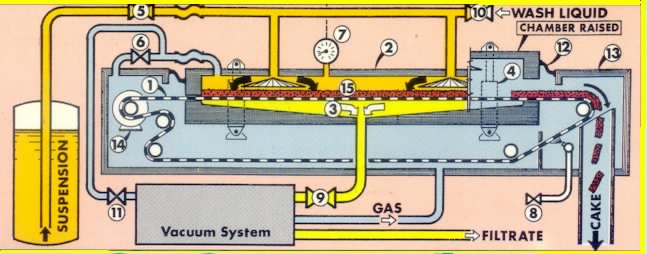
The above schema shows a fully contained but accessible Miller Vacuum Filter fitted with an endless band.
The patent discloses a sealed system with re-circulation of the gas and vapour internal environment.
The realisation of this stage of development ushered in the era of a filtration system that operates as the heart of many chemical and pharmaceutical plants.
|
 |
FILTRATION - THE PATENTED CHAMBER SEALING MILLER PRINCIPLE (GB 2280857)
|
 |
 |
|
The disclosure is made in GB 2280857 of a principle for chamber sealing by means of the ambient fluid surrounding a pressure filter of the type described in the preamble to Claim 1 and detailed in Claims 1, 4, 11, 12, 13 whereby means are described to apply pressure and/or vacuum to transfer contaminant and filtrate simultaneously and thereby achieve a secure seal concerning the egress of liquid from the filter chambers to the ambient atmosphere during the filtration cycle.
This patented principle is illustrated by the diagram on the right.
Miller Filters of this description have been installed for the filtration of a variety of chemicals many containing solvents.
Grades of Hastelloy are the common material of construction employed in these fabrications.
|
 |
|
 |
 |
 |
|
|
2000 -->: PATENTED INNOVATIONS AND REALISATIONS
|
 |
 |
 |
 |
|
The core vision of this development is summed up in the lead paragraph of THE JOURNAL OF THE FILTRATION SOCIETY, October 2002:
|
|
|
|
The Filtration Society / 2002
-THE NUTSCHE FILTER COMES OF AGE- Peter Miller
“An emerging technology is outlined that appears destined to play a major role in how liquids in the future will be purified in the major liquid processing industries. Instead of piecemeal tinkering with "case history" methodology accompanied by the proliferation of purification stages and a worsening of the environmental pollution problem, the possibility of a generic solution is now in the offing. The goal is the realisation of a liquid purification ROBOT. The paper outlines how this goal is to be achieved with reference to the chemical, pharmaceutical, beverage, food and water industries, whereby all waste stream pollution is to be eliminated at source. The R&D program to realise this goal is outlined with references to web-site detailed information including patents.”
|
|
|
|
The methods used in fluid processing and using industries are often rooted in the past. These industries comprise a large number of segments specialising in specific products (e.g. in the field of beverages: beer, wine, soft drinks, etc.) each of which perceives their own processes to be unique and not to be “tampered” with. The vision is to develop a cybernetic universally applicable type filter plant as the centrepiece of complete fluid processing operations in which innovative liquid purification and solids recovery systems will play a central role.
|
|
 |
|
 |
 |
 |
|
 |
- RESEARCH IN REGENERATIVE DEEP BED FLUID PURIFICATION
|
 |
 |
|
ACHIEVEMENT: Empirical investigations of deep bed liquid purification were carried out using a variety of granular materials in the size-range 50-500μ with the goal of regenerating and reusing the material of the bed to improve the economic viability of processes and eliminate present wasteful and environmentally damaging practices. A large number of preliminary tests were carried out to characterise the various bed materials, flocculants, coagulants and adsorbent materials for their potential use in liquid purification operations in the nano- / ultra-filtration and micro/macro particulate size ranges.
|
 |
 |
|
BED MATERIALS TESTED (Materials were fractionated to the mean sizes 20, 50, 100, 200, 500 micron)
|
 |
 |
|
MATERIALS CHOSEN FROM FOR FURTHER RESEARCH STUDY:
|
 |
- Quartz Sand
- Graded quartz sand with grain sizes 50-1000 micron
- Kieselgel
- Graded amorphous kieselgel with grain sizes 10-500 micron
- Kieselguhr
- Graded diatomaceous earth with effective particle sizes 20 – 300 micron
- “Perlite”
- Graded heat treated (roasted), ground silicate rock with effective particle sizes 50-500 micron
|
 |
 |
|
RESULTS: The results of this research study represent a key contribution to the realisation of the design and fabrication of bed regeneration systems for application in large industrial liquid and gas purification operations.
|
|
 |
|
|
THE SYSTEM
|
|
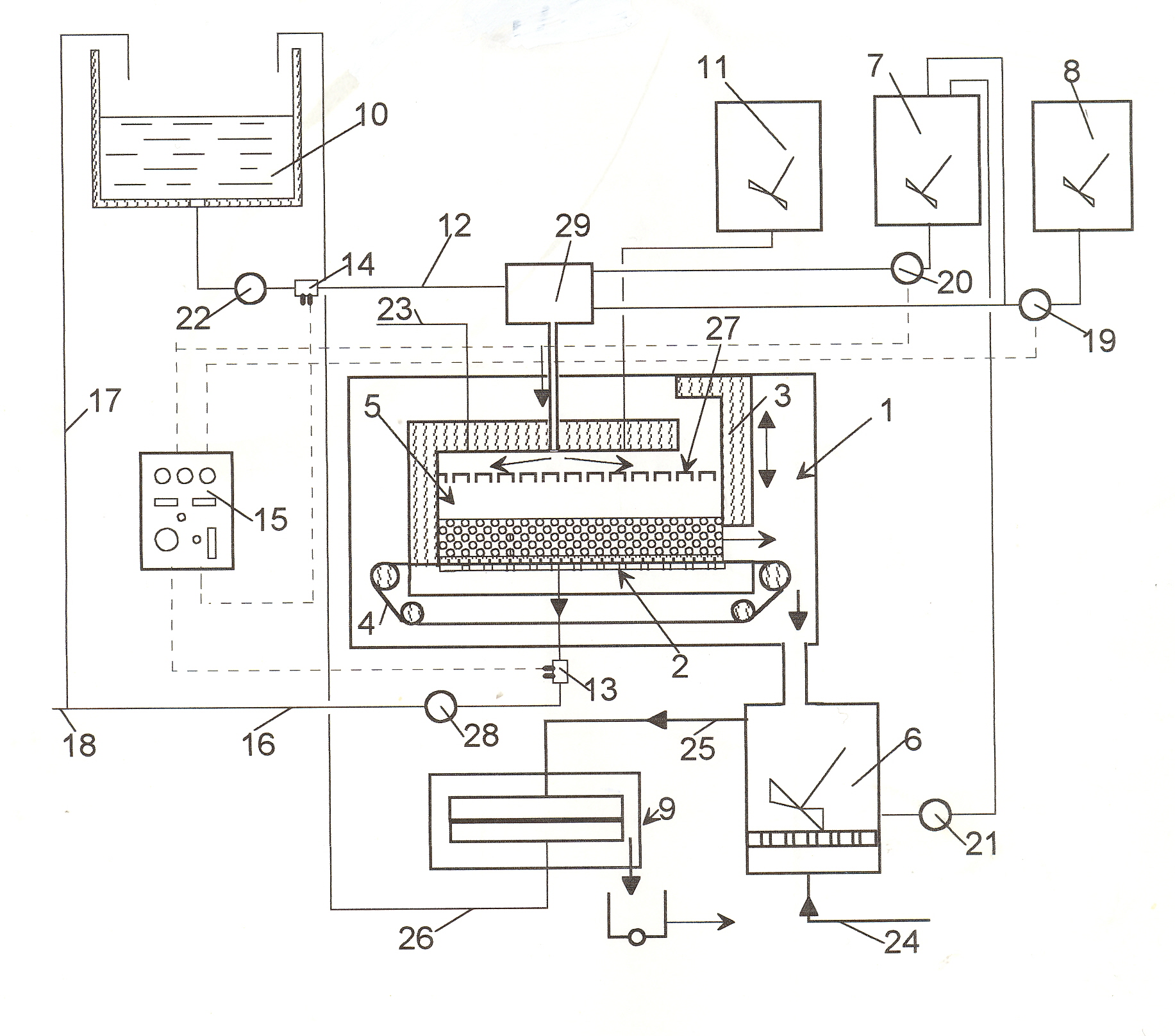 |
|
 |
 |
|
OPERATION: Beds after use are discharged to bed regenerator (6). After reslurrying the bed in special regeneration liquid the impurities are removed by classification carried out by passing clean liquid upwards through the bed (24). The backwash liquid, purified in filter (9), is recovered and recycled. The cleaned bed is reslurried in clean liquid and pumped (21) to hold tank (7) for reuse.
|
 |
- DEVELOPMENT OF SECTIONS OF EXPANDED FILTER MEDIA INTEGRAL WITH A FILTER BAND
|
 |
 |
|
THE MERGING BOUNDARIES IN FLUID PURIFICATION TECHNOLOGY
The requirements of the fluid processing and using industries concerning the purity of the fluids processed and employed are becoming increasingly demanding.
The technical distinctions and boundaries conventionally made between solid/fluid separation operations, ranging from applications where visible solids in suspension are separated to operations where adsorption and separation of molecular and/or atomic species from fluids are carried out are rapidly disappearing.
|
|
|
 |
 |
|
The demands of the liquid purification industries point to the need for REGENERABLE COMPACT EXPANDED MEDIA SYSTEMS to facilitate the rationalisation of these operations leading to automated universal application with zero environmental impact as well as a much improved cost-effectiveness of the operations.
|
|
 |
 |
|
The MILLER expanded surface belt filter shown schematically on the left was conceived to fill this purpose.
The strength of the design lies in the mobility of the expanded surface element enabling a gamut of methods of regeneration to be utilized that is completely failing with state of the art systems.
|
|
 |
|
|
|
 |
 |
 |
|
 |
|
 |
 |
 |
|
 |
|
 |
 |
 |
|
 |
 |
|
- DEVELOPMENT OF SECTIONS OF PACKED BEDS
INTEGRAL WITH A FILTER BAND
|
|
|
BACKGROUND: The employment of STATE OF THE ART packed beds as media for fluid purification and processing has had a chequered career. The SAND FILTER has found application almost exclusively in large-scale water purification. Its use even in this field has dwindled markedly over recent decades. Outside of water filtration the sand filter has found only rare application in the broad fields of fluid purification and processing. Although PACKED COLUMNS are used in the wider fields of liquid purification these applications can be classed mainly in the niche category. The use of CARTRIDGE FILTERS and PACKED ELEMENTS is restricted to small scale fluid purification and air conditioning. Perhaps the greatest hindrance to improvement with state of the art granular filters is the relatively static nature of the beds that causes insuperable difficulties in achieving bed regeneration.
|
 |
 |
|
MILLER MOBILE PACKED BEDS
|
 |
|
 |
 |
 |
|
 |
 |
|
FLUID PURIFICATION and CONTACTING PROCESSES
|
 |
As a result of the ultimate development phase of the Miller Filter far more compact and versatile apparatus and methods are now available in the form of MOBILE PACKED BEDS for rationalising the present bewildering array of apparatus and methods for contacting FLUIDS with beds for the purpose of
|
 |
- liquid purification,
- extraction,
- catalysis,
- ion-exchange
- liquid/gas reactions.
|
 |
 |
|
EXAMPLES:
|
 |
BED MATERIAL
|
FLUID PURIFICATION
|
EXTRACTION
|
CATALYSIS
|
ION EXCHANGE
|
LIQ/GAS REACTION
|
Activated carbon
|
Seeds (veg)
|
Metals: Ni, Pt, Agt
|
Cationic
|
Hollow spheres
|
Silica gel
|
Plant matter
|
Metal oxides, VD, Cr, Mo
|
Anionic
|
|
Kieselguhr / Bentonite
|
Malt
|
Al-silicates, AIO, Si-gel
|
Mixed
|
|
Fibreglass
|
|
|
|
|
Silica (sand)
|
|
|
|
|
|
 |
 |
|
D. UNIVERSALLY APPLICABLE FLUID PURIFICATION SYSTEM
|
 |
 |
 |
|
 |
 |
|
Background: State of the art fluid purification technology is dominated by numerous diverse “niche” solutions to problems that are seen as unique calling for unique “one-off” solutions. More recent global attention to matters dealing with ecological environmental pollution points to this sector as the major contributor to the present serious environmental situation.
One thing is now clear: The solution to the complex of problems ranging from excessive carbon emissions, polluted land, rivers, seas and air lies in the ability to RECYCLE all present emissions within the immediate processing operations.
The MILLER UNIVERSAL FLUID PURIFIER depicted below is designed to achieve this goal.
|
|
|
MILLER UNIVERSAL FLUID PURIFIER and SOLIDS RECOVERY
|
|
|
|
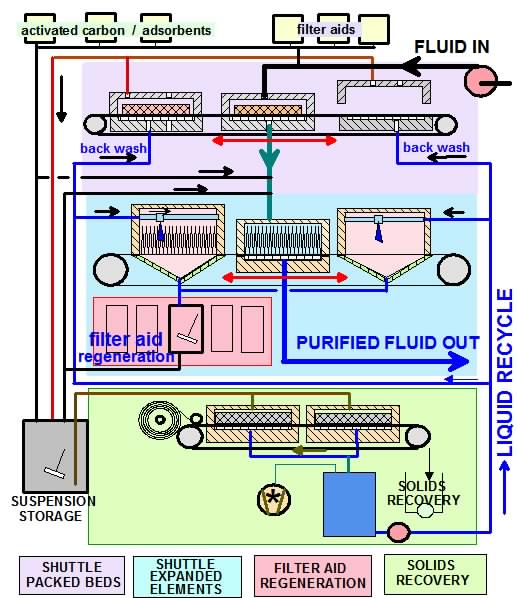 |
|
|
|
The FOUR innovative separation sectors:
|
|
|
- Shuttle packed beds
- Shuttle expanded elements
- Filter aid regeneration
- Solids recovery
|
|
covers practically all existing fluid purification and solids’ recovery requirements.
|
|
|
At present in the NANO-MICRO range of separation intractable media blockage problems are widespread in all sectors of large-scale industrial fluid purification operations and constitute the main causative factor of today’s serious global environmental problems. THE MILLER UNIVERSAL SYSTEM IS THE ANSWER TO THIS PROBLEM.
SHUTTLE PACKED BEDS Liquids: Optimal pre-treatment with flocculating, coagulating and adsorbent powders cause the adsorption and physical retention of sub-micronic particulate matter that are the main cause of media blockages of such operations as reverse osmosis. This clarification capability is out of the reach of conventional high-speed centrifuges. Gases: Pretreatment with electrostatic loading devices such as corona discharge cause the removal of sub-micronic particulate matter by means of surface pre-charged shuttle packed beds. The effective regeneration of these beds with the shuttle system explains the marked advantage over prior art deep bed purification methods.
SHUTTLE EXPANDED ELEMENTS Fluids: Filtration area densities of 50-100m2 /m2 floor space are necessary for large scale industrial fluid processes requiring separation in the NANO-MICRO particulate size range. Here again the purification technique does not rely on “pore” filtration but on surface adsorptive phenomena. The aim is to adsorb targeted submicronic particulate matter on electrostatically charged surfaces of finely divided beds of filter media such as kieselguhr and other silaceous matter supported on membranous expanded elements. Thereby in effect the membranous material can function in reverse osmotic mode without the danger of irreversible “blinding” of the pores. The shuttle function allows the application of element regenerative techniques based for example on ultrasonics to reverse mild “blinding” conditions in specially designed dedicated regenerative sections of the system.
FILTER AID REGENERATION The used thin beds from the shuttle expanded elements are sluiced into a separate system for regeneration and reuse. In effect this is a counter-current washing system whereby the impurities adhering to the surfaces of the particulate matter of the bed are removed. The regenerated bed material is recycled to the central filter station now containing a set of regenerated shuttle expanded elements to continue the operations with minimal delay.
SOLIDS RECOVERY Central to all liquid and solids processing industries are universally applicable solids’ recovery equipment. Total recycling of used fluids is dependent on the availability of such equipment. The basic Miller Filter design provides the possibility of full automation of operations previously associated only with manual operation.
|
 |
|
 |
 |
 |
|
 |
MILLER ROBOTIC SYSTEM & APPLICATIONS
|
 |
|
|
|
 |
 |
 |
|
 |
- PATENTS
|
 |
 |
|
GB2331027 ABSTRACT: This document describes complete systems for the fluid processing industries, whereby a universally applicable fluid purification and separation apparatus plays the central role in the production processes and fulfils all the requirements of modern fully automated product-dedicated as well as multi-product and multipurpose production facilities. It is further described how these systems will solve the present global problems associated with water and air purification on a large scale. Central to the solution of these tasks are two innovative purification elements illustrated by Fig.2 and Fig.3 that will play central roles in the systems here described for fluid purification and filtration in the particle size range of 10-10-10-5 m. Fig.2 is a schematic representation of a mobile regenerative packed bed element to be employed as mobile shuttle-groups integral with a movable band. Fig.3 depicts an innovative mobile regenerative expanded surface element also to be employed as mobile shuttle-groups integral with a movable band.
|
 |
|
|